1. Definition and history of the SMT
Surface mounting (SMT) is an advanced electronic assembly method that weld electronic components without pins or a small number of pins directly to the surface of a printed circuit board (PCB). This technology originated in the 1960s, and was first used by IBM in the manufacture of small computers, gradually replacing the traditional perforated welding technology. Although the initial development of SMT technology was relatively slow, by the 1990s, it had become the mainstream technology in the field of high-tech PCB assembly.
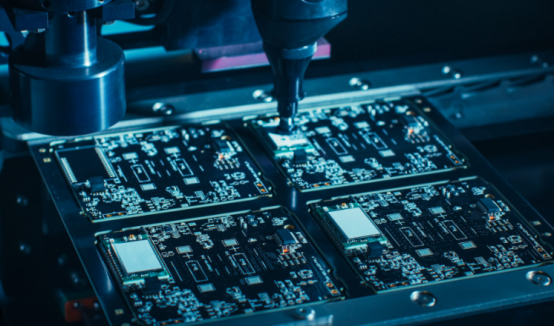
2. Critical equipment for the SMT technology
1. Plate fitting machine: As the heart of the SMT process, the plate machine is responsible for placing the electronic components precisely on the PCB.
2. Printing press: used for printing the solder paste on the PCB to provide the necessary bonding and conductive medium for the subsequent welding.
3. Testing equipment: including optical microscope and X-ray detector, used to ensure the quality of SMT components and welding integrity.
3. Process steps of the SMT
1. Preparation: including PCB preparation, the selection and placement of components.
2. Printing solder paste: use a printing press to accurately print the solder paste to the designated location of the PCB.
3. Patch: accurately mount the selected components to the PCB.
4. Welding: Use hot air or laser welding technology to firmly weld the components to the PCB.
5. Testing and repair: Check the quality of SMT components by testing the testing equipment, and make necessary repair to the defective products.
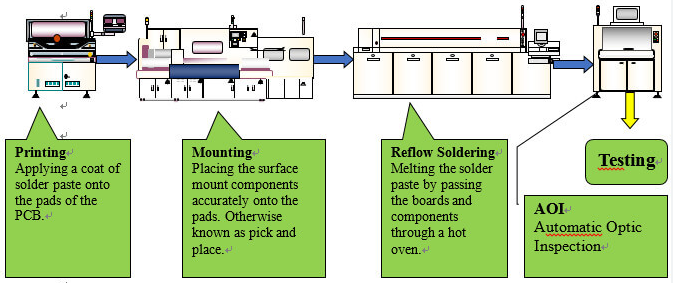
4. Quality control points of SMT
1. Process parameter control: strictly monitor the key process parameters such as patch speed, printing pressure and welding temperature.
2. Environmental control: Maintain constant environmental conditions, such as temperature and humidity, cleanliness, to prevent pollution and improve reliability.
3. Personnel training: strengthen the skill training of operators to improve production efficiency and quality awareness.
5. Advantages of the SMT automation equipment
1. Automatic patch machine: improve production efficiency and reduce labor cost.
2. Automatic testing equipment: real-time online testing to ensure production quality.
3. Data management system: monitor the production data in real time and optimize the production process.
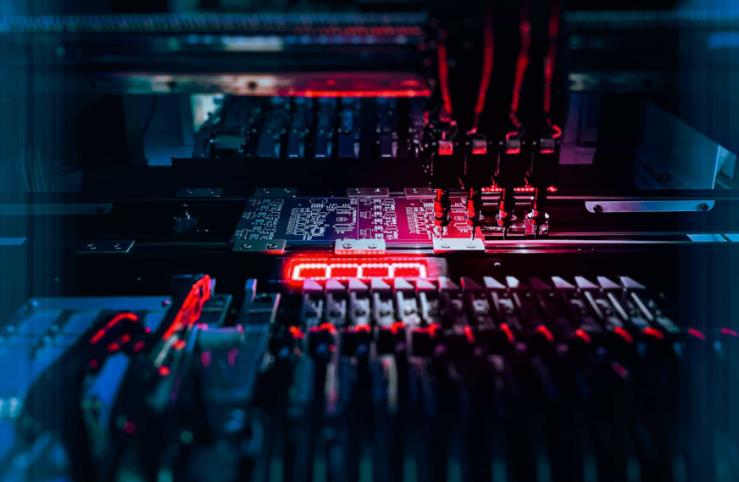
VI. SMT materials and their applications
1. Welder and paste: solder is used to form solder joints, and solder paste is pre-fixed SMC / SMD in reflux welding.
2. Solx: as the key flux for surface assembly, it affects the welding quality.
3. Binder: fix SMD in wave peak welding and double-sided assembly to improve production efficiency.
4. Cleaning agent: remove the welding residues and keep the product clean.
5. Tin paste: a mixture of solder powder and flux used in reflux welding.
6. SMT feeding belt: used to connect electronic components to reduce the downtime of the patch machine.
Through the integrated application of these technologies and methods, SMT technology not only improves the manufacturing efficiency of electronic products, but also ensures the high quality and reliability of the products, which has become an indispensable part of the field of electronic products manufacturing today.
I hope this article will give you a deeper understanding of ---------. I am your editor from TCWIN, guiding you on the road to lighting.